01/04/2024
Factory Final Inspection
BUSINESS NEWS | 14
Evaluating New Suppliers: Comprehensive Factory Final Inspection, Part.2
PHASE 5: Final Inspection
Ensuring Product Quality Before Shipment
Beyond in-process inspections, manufacturers must conduct final quality checks to ensure products meet the required standards before shipment.
- Conducting Final Inspections
- End-of-Production Checks: Quality control staff should conduct comprehensive final inspections of the merchandise at the end of production. This step ensures that any defects missed during earlier stages are caught, significantly reducing the likelihood of defective products reaching the customer.
- Thorough Evaluation: Final inspections should cover all aspects of the product, including functionality, aesthetics, and adherence to specifications.
- Adherence to International Standards
- Standardized Protocols: Following internationally recognized standards during final inspections ensures consistency and reliability. Compliance with these standards is crucial for maintaining product quality and meeting customer expectations.
- Global Best Practices: Implementing best practices from global standards enhances the credibility and marketability of the products.
- Documentation and Traceability
- Accurate Reporting: Quality control staff should accurately file and trace formal written inspection reports. Proper documentation ensures that any issues identified during the final inspection are recorded and addressed.
- Traceability Systems: Implementing robust traceability systems helps track inspection outcomes and maintain accountability, making it easier to identify and rectify any issues that arise.
Conclusion
By conducting thorough final inspections, adhering to internationally recognized standards, and maintaining accurate documentation, manufacturers can ensure that products are shipped with minimal defects. These practices are crucial for delivering high-quality products that meet customer expectations and maintain the manufacturer’s reputation for excellence.
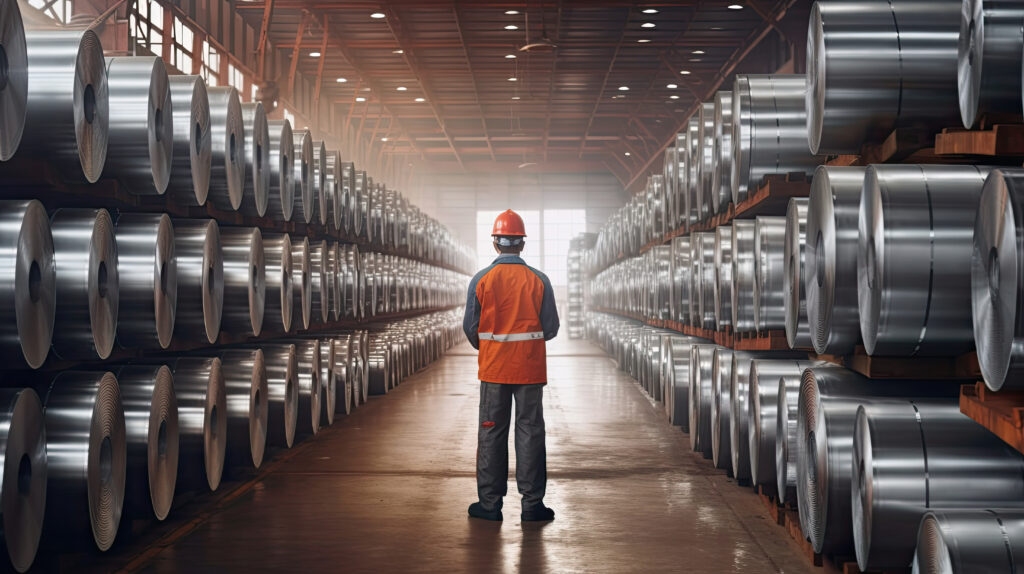
PHASE 6: Packaging
Ensuring Product Integrity Through Packaging
Packaging plays a crucial role in preserving product integrity and meeting shipping requirements. Attention to detail in the packaging process is essential to prevent contamination and ensure products remain in pristine condition.
- Clean and Organized Packaging Area
- Hygiene and Organization: The packaging area must be clean, organized, and free of contaminants. Maintaining a hygienic environment reduces the risk of product contamination and ensures the quality of the packaged goods.
- Contamination Prevention: Implementing measures to prevent contaminants such as dust and dirt from entering the packaging area is crucial for maintaining product integrity.
- Accurate Carton Placement
- Preventing Misplacement: Measures should be in place to prevent products from being placed in the wrong cartons. Accurate carton placement ensures that products are correctly packaged and shipped to customers without errors.
- Quality Control Checks: Regular quality control checks during the packaging process help identify and rectify any errors or discrepancies in carton placement.
- Worker Protection and Contamination Prevention
- Protective Clothing: Workers involved in the packaging process should wear gloves or other protective clothing to prevent contamination. This minimizes the risk of product contamination and maintains hygiene standards.
- Training and Awareness: Proper training and awareness programs ensure that workers understand the importance of maintaining cleanliness and following hygiene protocols during packaging.
Conclusion
Maintaining a clean, organized packaging area, implementing measures to prevent misplacement of products, and ensuring worker protection are essential for preserving product integrity during packaging. Effective packaging practices contribute to maintaining product quality, meeting shipping requirements, and upholding the manufacturer’s reputation for excellence.
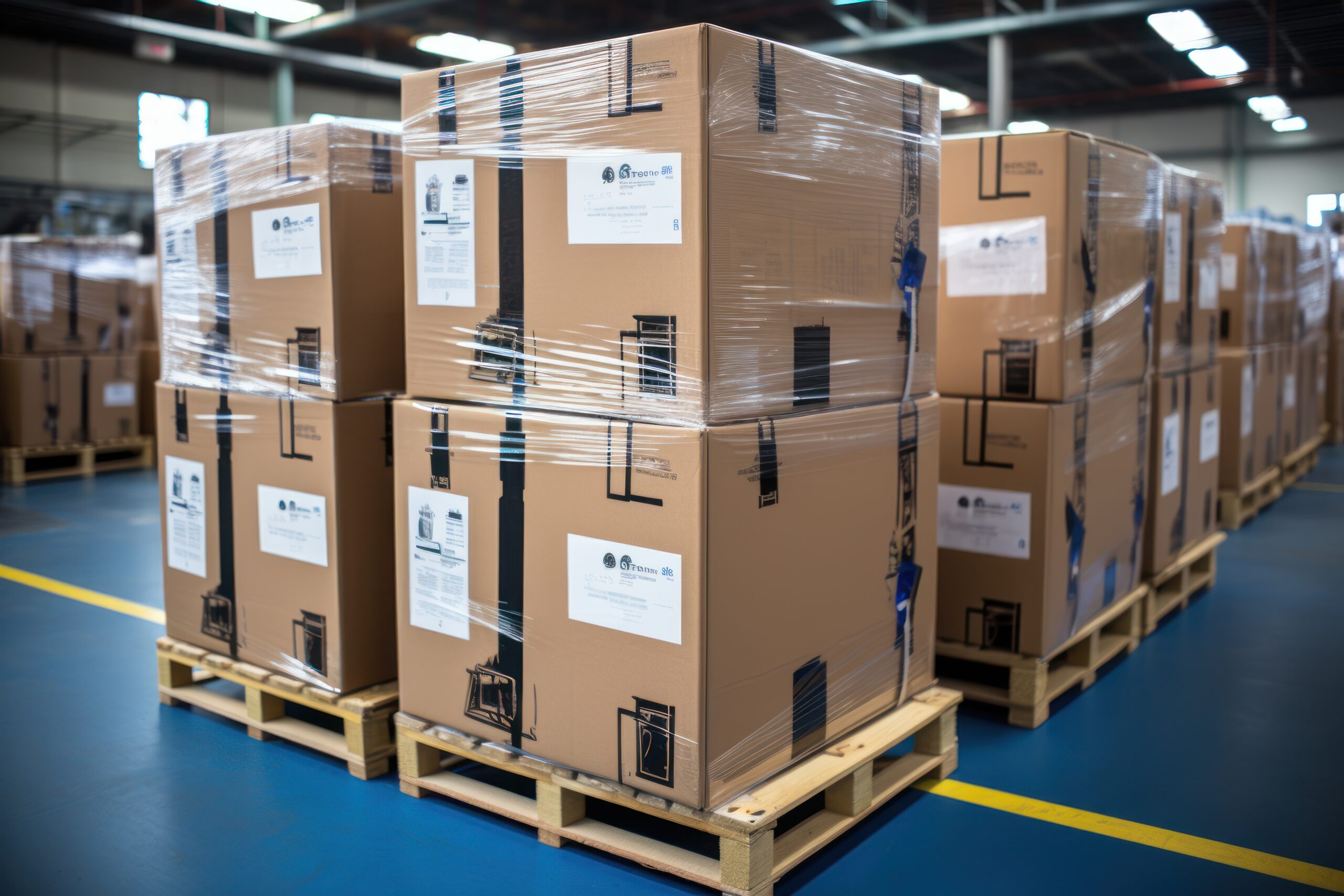
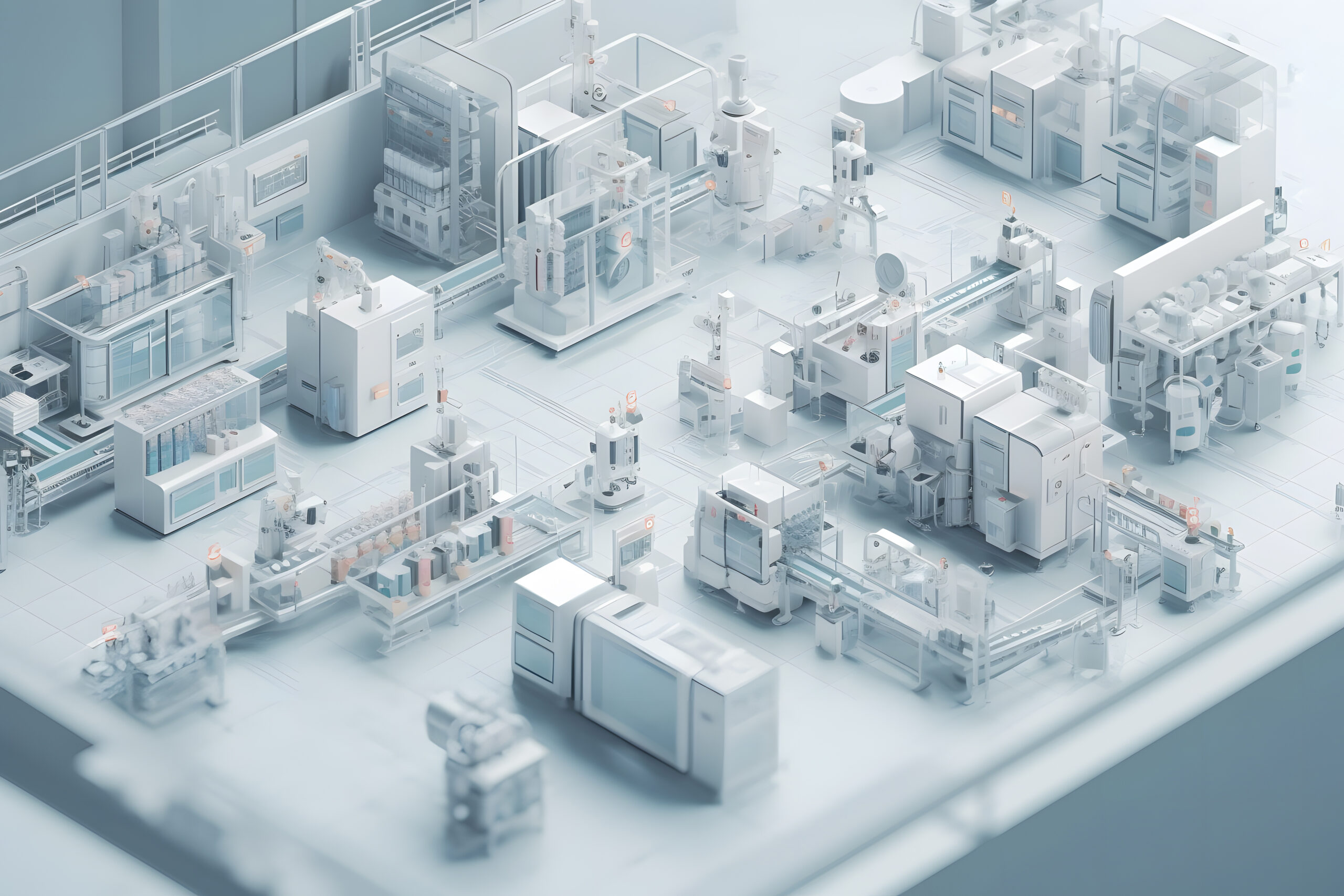